EndoGas production using microwave heating with temperature control
Summary
The project idea is to use controlled process of the selective zone heating inside of catalytic reactor by microwaves (MW) instead of contact or contactless (radiation) heating through the reactor wall.
Special designed Multichannel High Temperature Meter (MC-HTM) will be used to control temperature inside the reactor, in exchange for traditional thermocouples, which have strictly limited application area in presence of strong electromagnetic fields.
Preliminary experiments showed the feasibility of microwave heating of the catalyst unit and demonstrated positive feature of this scheme to prepare EndoGas, Table1.
H2, vol % | CO, vol % | CH4, vol % | CO2, vol % | Tout, ° C |
39.8 | 20.1 | 0.4 | 0.2 | ~900 |
Introduction
Catalytic partial oxidation (CPO) of methane and other hydrocarbons is an effective technology for the production of synthesis gas, which in turn can be used as hydrogen source for fuel cells, to develop gas-to-liquid technologies, as a protective atmosphere for thermochemical treatment of metal parts (EndoGas) and so on. The standard approach is the external heating of catalytic reactor to achieve required operating temperature, typically about 1000oC. In these reactor designs, temperature heterogeneity in the catalyst affects the quality of produced mixture. Commonly used catalysts are porous medium (filling, mesh, and honeycomb).
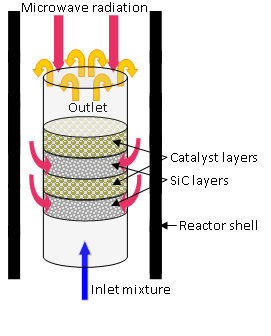
In HMTI a number of problems were revealed. When external heating is applied in such reactors, it is difficult to avoid temperature gradient. To obtain the desired composition of CPO products it is necessary to use an excessive amount of catalyst used and overheating of catalyst outer layers adjacent to heated reactor shell. Preheating of inlet mixture somewhat reduces the problem, but it is limited due to the risk of fire of working mixture at reactor inlet. Also in this arrangement, superheated zone (by 100 - 150°C above the target operating temperature) is formed in the inlet part of the catalyst where the accelerated degradation of the catalyst occurs.
Since the endothermic part of CPO process requires heat input into the reaction zone, the ideal solution would be distributed over the volume the input of heat instead of heating through reactor shell. For this purpose it is possible to use MW radiation, if to fabricate catalyst unit appropriately (Fig.1). Application of high (GHz-range) frequency electromagnetic waves to deliver energy to chemical reaction zone has a lot of advantages:
- direct heating of required volume;
- as consequence, fast start (tens of minutes) of process and high performance index;
- necessary space distribution of energy release could be reached;
- clean, ‘contact-free’ operation;
- lifetime of solid-state MW generator - 10 years and more.
Project Objectives
The general objective of project is a design, manufacture, test and delivery to Customer of CPO MW set-up and performing research program using this equipment. Core part of this set-up is the catalytic partial oxidation reactor equipped with microwave heating (CPO/MW-reactor) and having temperature feedback by using of original Multichannel High Temperature Meter with strong EMI immunity.
Multichannel high temperature meter with strong EMI immunity
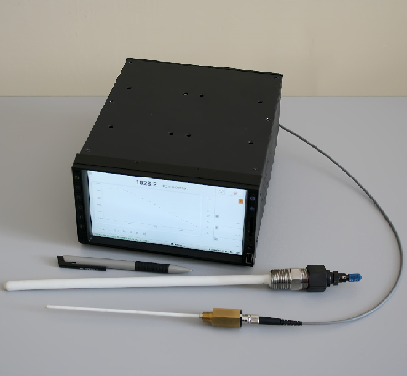
MultiChannel High Temperature Meter (MC-HTM) is designed to replace traditional temperature sensors as thermocouples, thermoresistors etc. for high (> 600oC ) temperature areas in presence of strong electromagnetic fields. Application area: microwave and inductive heating, high voltage equipment, intensive electromagnetic interference (EMI) environment and so on.
Optical system of MC-HTM collects light irradiation from the bottom of standard Ceramic Thermocouple Protective Tube, transfers it by fiber optics to MEMS (microelectromechanical systems) – based multichannel optical switch and then into a spectrophotometer. The temperature is defined as a parameter of the detected spectral distribution in visible/near-infrared range by direct fitting the data of the spectrophotometer to Planck's law.
This design of MC-HTM allows measuring the temperature profiles, having up to 24 or more independent channels in the temperature range 600oC - 2300oC with accuracy of 0,5%, keeping the calibration parameters over long time of operation.
Key distinctive features/advantages of MC-HTM are:
- be able to work where others cannot – at microwave oven, under high voltage potential etc.;
- long-term stability, the reading does not depend of optical signal amplitude and then from contamination/degradation/misalignment of optical parts;
- high temperature operation, upper bond is limited by protective tube material.
Channels number | 4 |
Temperature range, ° С | 600 – 2300 |
Accuracy, % | 0.5 or better |
Calibration interval | one year |
Thermoprobe dimensions: | |
Working part external diameter, mm | 3-19 and more; |
Working part length, mm | 150-600 and more |
Control Unit: | |
Dimensions, mm | 225x180x112 |
Weight, kg | 2.2 |
Length of connecting fiber optic cables, m | 5 and more |